Ultrasonic level meter model selection 6 points
Ultrasonic liquid level meter is a common non-contact liquid level meter. It has a wide range of applications in petroleum, chemical, electric power, sewage treatment and other industries, but many new users are still prone to errors in the selection, resulting in the purchase of products. The effect is poor or even impossible to use, then the following 6 points should be noted when selecting the ultrasonic level gauge.
1. Pay attention to the range and blind zone
The range and dead zone are two important indicators that reflect the ultrasonic level gauge. The range is the maximum range that can be measured. Reflects the sensitivity of the transducer. In other words, the larger the range, the higher the sensitivity. The blind spot is an important indicator to reflect the quality of the transducer. The blind zone is also called the dead zone, a distance that the ultrasonic level gauge does not measure, which is caused by the aftershock of the ultrasonic transducer. Then the smaller the blind zone of the same range of products, the better the design of this transducer. For some closed tanks or short range measurements, the installation will be more convenient. Therefore, the blind zone becomes an important indicator for measuring the performance of the transducer in the same range of products.
2. Pay attention to the temperature and accuracy of the measured medium
Most of the temperature range is nominally -20~60 °C. Because most of the liquid level display level meter, the operating temperature of the LCD screen can only be in this range. Beyond this range, the liquid crystal display will be abnormal. If you do not consider the limitations of the liquid crystal display, you can generally achieve a range of -40 to 80 °C.
Why put the accuracy and temperature together, because in the air, the temperature measurement error is 1 °C, the effect on the speed of sound is 0.6m / S, 20 ° C, the sound speed is about 340m / S at 1 atmosphere. Therefore, it can be calculated that the influence on the measurement error is 0.17%, that is, if the temperature measurement error is 3 °C, the level measurement error exceeds the nominal range of 0.5% of most manufacturers. Therefore, the actual accuracy of 0.5% is for normal temperature and pressure. For both high and low temperatures, it is possible to cause measurement accuracy of more than 0.5%. When there is a temperature gradient and the temperature changes rapidly, the measurement error will also increase. In addition, the most important influence on the measurement accuracy is the gas composition. That is to say, in the case of some volatile liquids, the composition of the air changes due to the volatilization of the liquid, which in turn leads to measurement errors caused by changes in the speed of sound of the gas.
3. Pay attention to the pressure on the measurement site
In the case of negative pressure, ultrasonic measurements are generally not recommended because ultrasonic propagation is achieved by gas. Negative pressure means that the air inside is thin, and the ultrasonic wave propagates under the thin air. One is that the speed of sound will change, causing measurement error. The other is that in the thin air, the attenuation of the sound wave increases, resulting in a decrease in the measurement range or even measurement. The positive pressure is mainly the effect of the probe structure as long as there is no problem with the probe structure. Does not cause air leakage. Then the ultrasonic level gauge can work under large pressure conditions.
4. Pay attention to the measurement environment and whether the medium is corrosive
The corrosiveness of the level meter mainly tests the material of the probe. In the environment of weak acid and weak alkali, ordinary plastic casing can be used. With a PTFE shell, it can withstand most of the strong acid and alkali. It should be noted here that if the substance to be tested is relatively corrosive and volatile, it is better to glue the board when using a one-piece level meter. Because most of the waterproof housings are not resistant to gases. When the gas enters the unit, it will corrode the board.
5. Pay attention to the installation orientation and installation structure
The mounting structure is generally available in both flange and threaded versions. Lifting is not recommended. Because the lifting is easily affected by the wind. However, when installing, it is generally necessary to consider the impact of the blind zone. We must physically ensure that the distance from the highest liquid level to the probe surface is greater than the dead zone. In order to avoid the blind zone, when installing with an elongated conduit, it must be noted that the angle formed between the two ends of the probe radiating surface and the end faces of the duct must be greater than the sharp angle of the transducer.
6. Pay attention to the power supply mode and signal output mode
The power supply mode is generally AC power supply 95~230VAC, 24VDC
Four-wire system, 24VDC two-wire system. The output modes are: display interface, current 4~20Ma, communication mode 485 communication, Hart communication, etc.
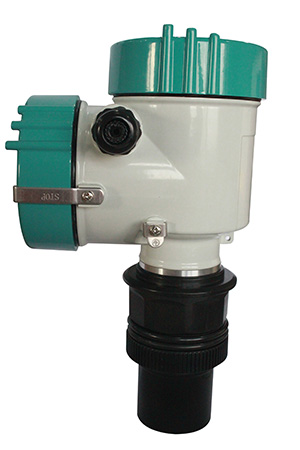